Wasp Barcode Technologies: The Barcode Solution People
The Best Companies Move Beyond Spreadsheets
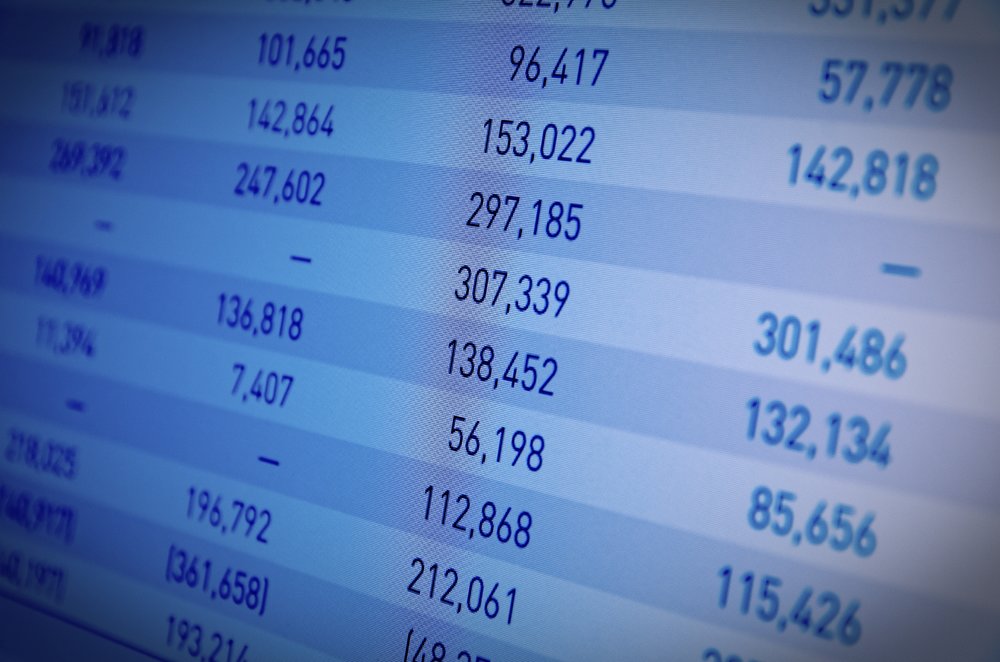
In a perfect world, everyone would use automated
inventory management software to track when new shipments come in, when orders need to go out and every step in between. Many companies, however, have chosen to stick with manual processes, such as adhering to Excel spreadsheets, either because they don’t view their current method as problematic or they don’t see marked value in upgrading.
[su_divider top="no" size="2"]
[su_divider top="no" size="2"]
To a point, that can be accurate. For some companies, many of them small or home-based businesses, their system isn’t complex enough to require automation. They can remember to make changes to their inventory records after every transaction, and can also account for needed restocks, transaction history and everything else that goes into running a company on the fly or from memory. There’s a reason that large retailers like Amazon and Wal-Mart use barcode labels and scanners rather than spreadsheets to track their inventory: They are simply too large and successful to waste time with the grey areas that arise from using manual processes.
Yet most businesses haven’t gotten that memo, which is likely a big reason why they don’t see the kind of groundbreaking success that Amazon has, the kind of success that makes it possible to literally keep their inventory randomly organized while moving at peak efficiency. The decision to stay away from automated inventory management, whether conscious or not, is surprisingly common: the Wasp Barcode State of Small Business Report says 46 percent of businesses polled either use a manual process to track inventory, or don’t do so at all. Other polls put the percentage of midsize or large companies that have stuck with spreadsheets at 70 percent, despite often noting that spreadsheets are the source of consternation when planning for the future.
[Tweet "46 percent of businesses polled either use a manual process to track inventory"]
The truth is, there is a thin line between success and failure in today’s increasingly competitive and global economy. To become a giant, or even a moderate success, in almost any industry, a la Amazon in retail, moving away from spreadsheets is likely a requirement, for a few reasons.
Accuracy
Diligent bookkeeping is a requirement for a successful business, and no matter how careful those in charge of recording inventory are, mistakes are inevitable when using spreadsheets. Studies show that as much as 88 percent of all spreadsheets contain “significant errors,” which in some causes were devastating enough to cause billions in losses. The risk of financial catastrophe based on false calculations is still very real, according to Grenville Croll, a spreadsheet risk expert:
"Spreadsheets have been shown to be fallible, yet they underpin the operation of the financial system. If the uncontrolled use of spreadsheets continues to occur in highly leveraged markets and companies, it is only a matter of time before another 'Black Swan' event occurs causing catastrophic loss."
Inaccurate spreadsheets are financially devastating on a number of levels, not just for highly valuable corporations. Medium-sized and small businesses can feel the burn in the following ways:
- Inflated carrying costs of inventory: Inaccurate inventory records may mean you are paying more for “carrying costs," such as fees for storage space, insurance costs, depreciation (which may lead to write-offs and other unnecessary losses), opportunity cost and more.
- Taxes: When conducting audits for tax purposes, businesses must account for the inventory they have on hand. Unnecessary stores of inventory, held on to “just in case” there’s a surge in demand, rather than “just in time," create higher tax bills.
- Customer service: The ability to track an item’s exact location, using a combination of GPS technology and barcode scanners along the route, as it leaves your warehouse and ends up at a customer’s doorstep has become the gold standard. Any hiccup in that process (a lost package, an incomplete order) can be devastating for your customer service reputation. Considering how much more expensive it is to “buy” new customers, rather than continue business with existing ones, that’s a hit many businesses can’t weather.
Collaboration along the supply chain
Collaboration among many people working in multiple places is crucial as remote, cloud-based computing becomes standard and supply chain management (every step of the inventory process from the delivery of raw materials to the warehouse to the delivery of a finished product) continues to grow in import and complexity. Excel spreadsheets are not built for collaboration of this magnitude, and as a result records are often inaccurate, with multiple versions of the same spreadsheet spawning and multiplying the intensity and reach of the errors. A system that updates on the fly automatically is a better fit for companies with workers spread out between the warehouse and the office, or sites in different states or even countries.
Forecasting
As mentioned above, inventory holding cost inefficiencies can be costly for several reasons. One important feature of automated inventory management systems that spreadsheets simply can’t match (save for taking the time to manually pore over old spreadsheets and records, a time-consuming endeavor that still runs the risk of inaccuracy) is the ability to properly forecast expected surges in demand. Companies like Amazon use the big data afforded to them by automated inventory management to know what products sell the best, when they sell the most, and what people often buy along with that item. As a result, they rarely worry about stockouts, or having to hold on to inventory they thought would sell but instead is deteriorating on their shelves. Accessing historical trends is much easier with a system that is designed to identify such patterns, rather than trying to collect the data manually.
The most successful companies aren’t the ones with the hardest working employees or the most luck or some secret algorithms that exploit market loopholes. If that was the case, there would be more successful businesses in the world, many of us work hard and oftentimes that simply isn’t enough. Great companies are the ones that embrace advances in technology to the fullest, making their employees as efficient as possible and allowing them to work smart as well as hard. Past a certain point, companies must stop relying on guesswork, estimates and gut feelings, especially in areas of business that require cold, hard calculation like inventory records and forecasting. To become an industry giant, you have to avoid the mistakes that so many of your peers make, and that starts with staying manual when the world is going automatic, digital, cloud-based and collaborative.
How would moving beyond a spreadsheet to an inventory management system help the accuracy of your inventory count?