Wasp Barcode Technologies: The Barcode Solution People
Preventing Supply Chain Fraud with Asset Tracking Software
Fraud takes on many forms as it silently creeps through the global supply chain in search of its next victim. Sometimes it starts with a supplier who falsifies labor expenses and exaggerates bills. Other times it’s an employee who pumps up his expense account or a contractor who promises kickbacks to an employee for using his services. Increasingly, fraud is threatening the global supply chain as counterfeiters thrive across the Internet.
One solution,
asset tracking software, can combat supply chain fraud by tracing where the product is as it moves across the supply chain. But are companies willing to take on this due diligence to protect their products? Careful research into global fraud confirms anti-counterfeit technologies are worth implementing.
Fraud continues to climb.
According to the
Bureau Van Dijk, supply chain fraud cases around the world saw a significant increase in the first half of 2013 with incidents totaling over $800 billion—a 28 percent increase from the same period the previous year.
And it continues to climb. According to the
2013/2014 Kroll Global Fraud Report, “The steepest ascent was in vendor, supplier, and procurement fraud. Other major sources of fraud included theft of physical assets (28 percent), information theft (22 percent), and internal financial fraud (16 percent).”
What is fueling fraud’s rising dominance? Experts agree—all roads lead to big data.
[su_divider top="no" size="2"]
[su_divider top="no" size="2"]
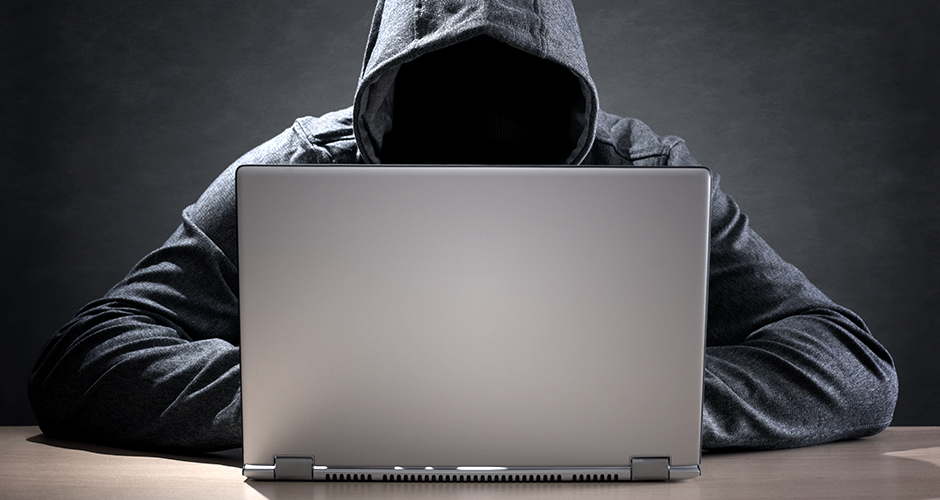
Item-level details fuel fraud.
A surprising number of business executives are leaving their supply chains vulnerable to fraud, according to a study by
Deloitte Financial Advisory Services.
“Part of the problem lies with the nature of “big data”—the existence of so many inputs that companies are having a tough time sorting through the noise and deriving information of value,” explains Deloitte principal Mark Pearson in a recent
Forbes article. “Companies are doing a better job of identifying high-level trends in invoice characteristics than they are scrutinizing individual line items. But the latter is where most of the fraud resides.”
Companies often operate in silos, exacerbating the problem. For example, the department that selects a vendor and signs the contract differs from the one who pays the bills. The vendor may summarize his services upon invoicing, making it difficult to tie expenditures back to the original contract and impossible for a forensic accountant to audit.
[su_divider top="no" size="2"]
[su_divider top="no" size="2"]
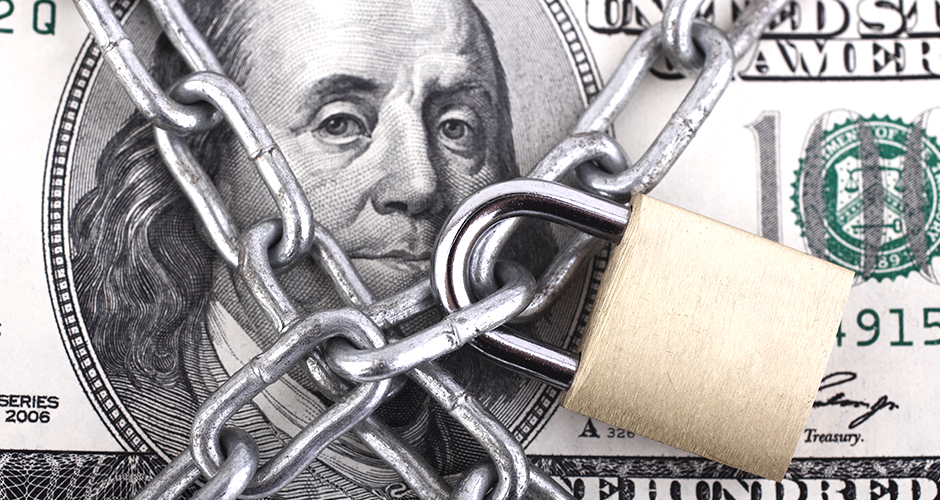
So does a lack of protection for intellectual property.
Although projected to fundamentally change how companies conduct business, big data and the
Internet of Things (IoT) are unwittingly promoting fraud outside of the four walls as well.
Stuart Rosenberg explains how manufacturers—not the criminal underground—have contributed to the onslaught of counterfeiting. “The Internet has turned counterfeiting into a low risk market by allowing groups unlimited access to the global market, low-cost communications, and free access to information of proprietary or confidential nature. The efforts to protect intellectual property have been largely ineffective due to organizations all too eager to share their standard operating procedures, transfer tooling, and quality manufacturing training ideas.”
Much has been written about
the importance of security with the onset of the IoT. As big data moves in and more networks are interconnected across the world, protecting intellectual property—while providing required
supply chain visibility—becomes vital. Yet, many organizations are resistant to anti-counterfeit technologies. Rosenberg explains: “Suppliers, vendors, and distributors are reluctant to collaborate, believing that sharing will diminish their value to manufacturers and lose business.”
Deloitte’s findings support this claim. “Only 12 percent of respondents are monitoring third parties for fraud, waste, and abuse on a quarterly basis, while 13 percent said they do it annually.”
[su_divider top="no" size="2"]
“Only 12 percent of respondents are monitoring third parties for fraud, waste, and abuse on a quarterly basis, while 13 percent said they do it annually.”
[su_divider top="no" size="2"]
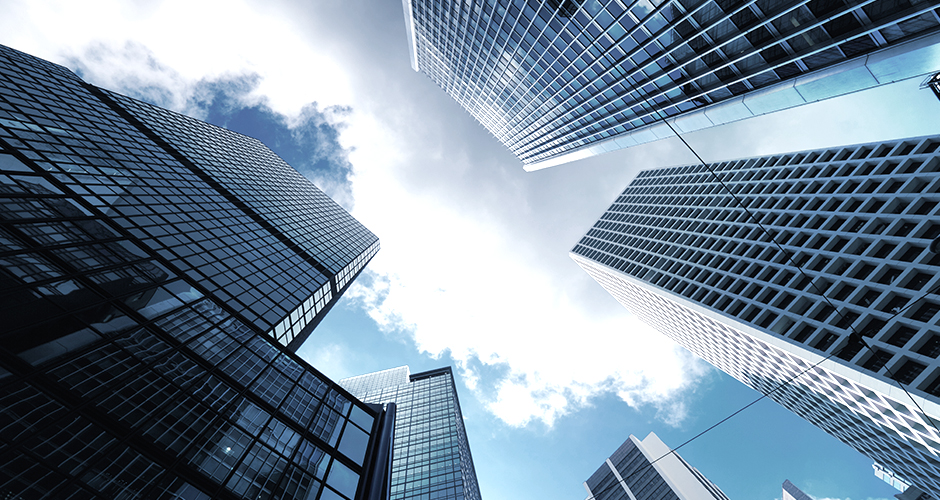
What can companies do?
“Being able to join up the dots using the most relevant information is a key tool in developing an informed picture, which will prevent risks,” adds Bureau Van Dijk. Both Rosenberg and Deloitte agree that organizations can wipe out fraud in supply chain relationships and counterfeiting if they are willing to use available tools and expertise.
Topping the list is analytics.
“Analytics can go a long way toward smoking out the miscreants,” explained Deloitte partner Larry Kivett in the Forbes article. “Tools for parsing the numbers are more sophisticated than ever. There’s a proliferation of data that didn’t exist five to 10 years ago. What’s more, as fraud investigators, we’ve gotten smarter about fraud schemes.”
To establish an analytics framework, Deloitte suggests these steps, which it describes in more detail in this
infographic:
- Identify an analytics strategy that includes business goals and drivers and key performance metrics (KPIs).
- Create an analytics solution, which considers sources of internal and external quantitative data and ideal analytical models.
- Integrate operational data into the business by linking the solution to business operations and functions, while making necessary process flow changes.
- Update and integrate technology to support faster implementation of new analytics tools.
- Manage change by encouraging buy-in and educating users.
- Measure performance against KPIs and follow up, as needed.
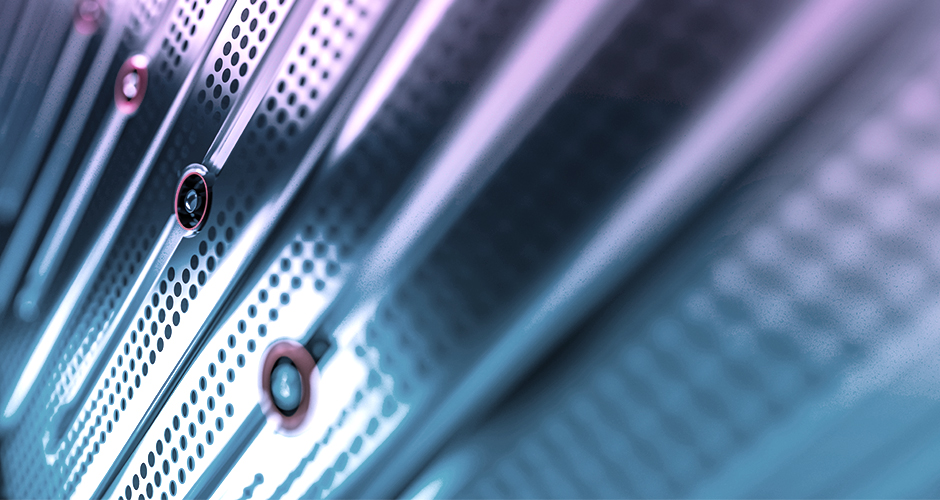
Technology drives analytics…and results.
Although each step is required to successfully implementing analytics, integrating technology is one of the most important.
Many organizations already use automatic identification and data capture (AIDC) solutions to streamline everyday processes, such as
inventory management,
asset tracking, warehouse management, and product management. But AIDC advancements in track-and-trace solutions, network security, wireless communications, and mobile scanning devices are changing how companies operate.
Instead of using a corded laser barcode scanner to simply read barcodes, companies are opting for
wireless mobile computers or
hands-free RFID readers that enable true workforce mobility across the global supply chain. With these sophisticated devices, today’s organizations can instantly capture information about products, parts, and people in real time and share it across the enterprise on integrated, high-speed networks. Not only can companies see where everything is and what it’s doing, they can view these activities in relation to everything else. This gives decision-makers the insight they need to easily achieve their goals. And, it provides end-to-end tracking and tracing that prevents fraud and ensures compliance with federal mandates.
Rosenberg is also a proponent of increasing control of production materials using track-and-trace technologies that record and analyze upstream and downstream movements across the supply chain. In support of that, he advocates the use of unique identifiers on barcode labels that track product movement or retrace the chain of ownership to prevent counterfeiting, along with sensory and digital authentication and other
anti-theft labeling solutions.
Sensory authentication uses overt and semi-overt package markings, such as color-changing inks or holograms to thwart counterfeiters, while digital authentication adds forensic markings that are authenticated by package or product scans using barcodes. Track-and-trace solutions require the largest investment because of their multilayer approach to product security.
With many options to choose from, companies no longer have to fall victim to supply chain fraud. By tracking assets across the supply chain, companies are strengthening the security of their products and the integrity of their business.
To learn more about fraud prevention solutions or to purchase asset tracking software, contact System ID at 888.648.4452.